The injection molding is plastic materials in the injection molding machine in the barrel through external heating and the rotation of the screw shear heat generated by the resin materials into the melt. By applying a certain pressure, the melt is injected into a certain cavity shape. After cooling and shaping, the product is injection molding.
The injection molding process is a common method of molding plastic products, and injection molding is a cycle process. The completion of injection molding needs to go through pre-plastic measurement, injection filling mold, pressure filling, cooling to finalize the 4 major processes.
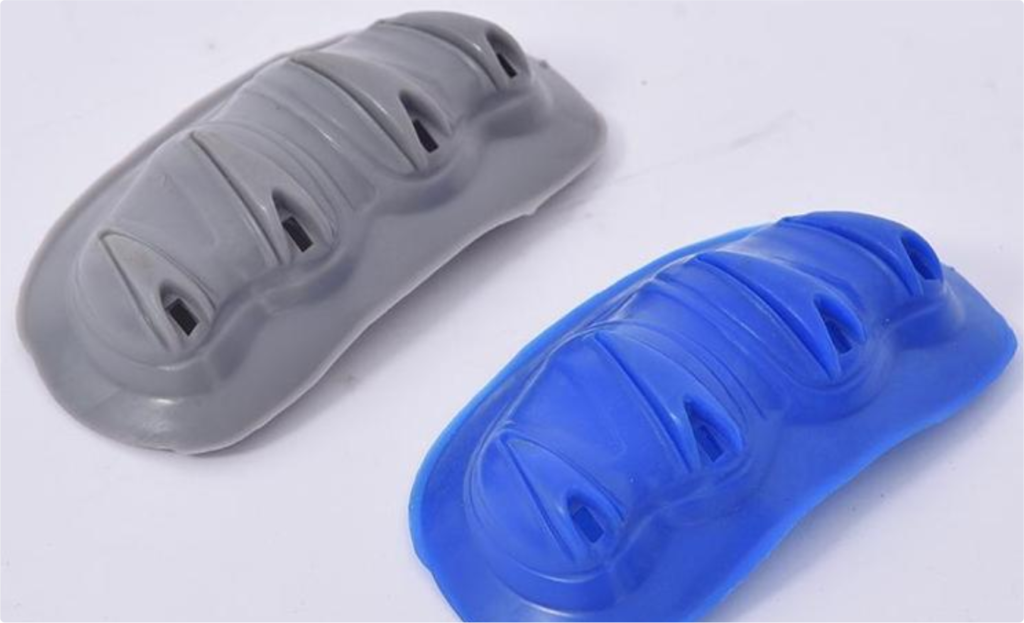
(1) pre-plastic stage
The screw begins to spin, then from the hopper and plastic to screw the front end, plastic under high temperature and under the action of shear force uniform plasticizing and gradually gathered in the front end of the cylinder, with the accumulation of the molten plastic pressure is bigger and bigger, finally overcome the screw back pressure will gradually push back when the plastic front cylinder reaches the required injection quantity, the stop screw back and roll, The pre molding stage is completed.
(2) Injection molding stage
The screw moves forward under the action of the injection cylinder, pushing the plastic stored in the front of the barrel forward at multiple speeds and pressures through the runner and gate into the closed mold cavity.
(3) The process of maintaining pressure and feeding
The injection pressure in the pressure holding stage is called the pressure holding pressure. Under this pressure, the melt in the mold cavity is fed due to cooling, and the product is compressed and densified. In this process, holding pressure plays a leading role.
The characteristics of the pressure holding stage are:
- The melt flows slowly under high pressure.
- The screw has a tiny feeding displacement.
- The material gradually takes shape with the cooling and density increase.
In the pressure holding stage, the melt flow rate becomes very small and does not play a leading role, while the pressure affects the process. In the pressure holding stage, the pressure and specific volume in the mold are constantly changing.
(4) Cooling and setting stage
The plastic is held in the mold cavity to prevent the reverse flow of the plastic until the plastic solidifies and the pressure in the cavity disappears. The proportion of cooling setting time in a production cycle is the largest.
It is mainly used for heating the barrel and nozzle. The cooling system is mainly used for cooling the feeding section of the mold, hydraulic oil and the barrel.