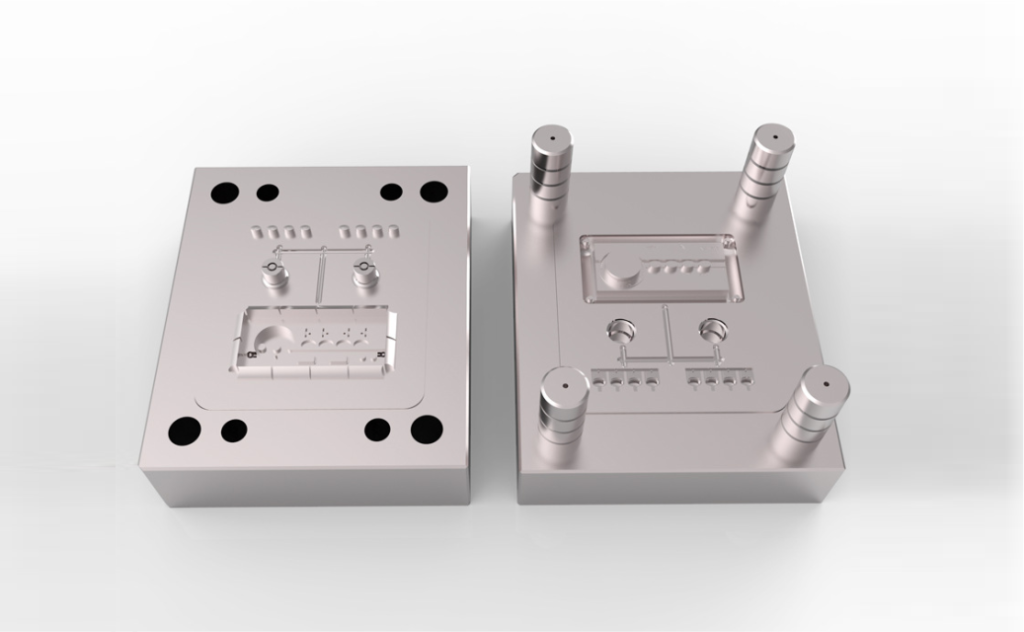
For injection molding mould designers, how to design the injection mould structure optimization as soon as possible according to the design or product requirements is the most important. Injection mold design needs to consider many factors, such as plastic type, plastic parts characteristics, cavity number, machine type and injection mold processing technology feasibility and so on. Injection molding tools, after the full study of these problems, you can start to mould design, injection mold design mainly includes the following aspects:
① Determine the number and arrangement of cavity;
② Determine the position and form of parting surface, runner and gate;
③ Disposition of lateral concave and convex and determination of push-out method;
④ Determine the processing mode of the mold;
⑤ Determine the way of temperature adjustment.
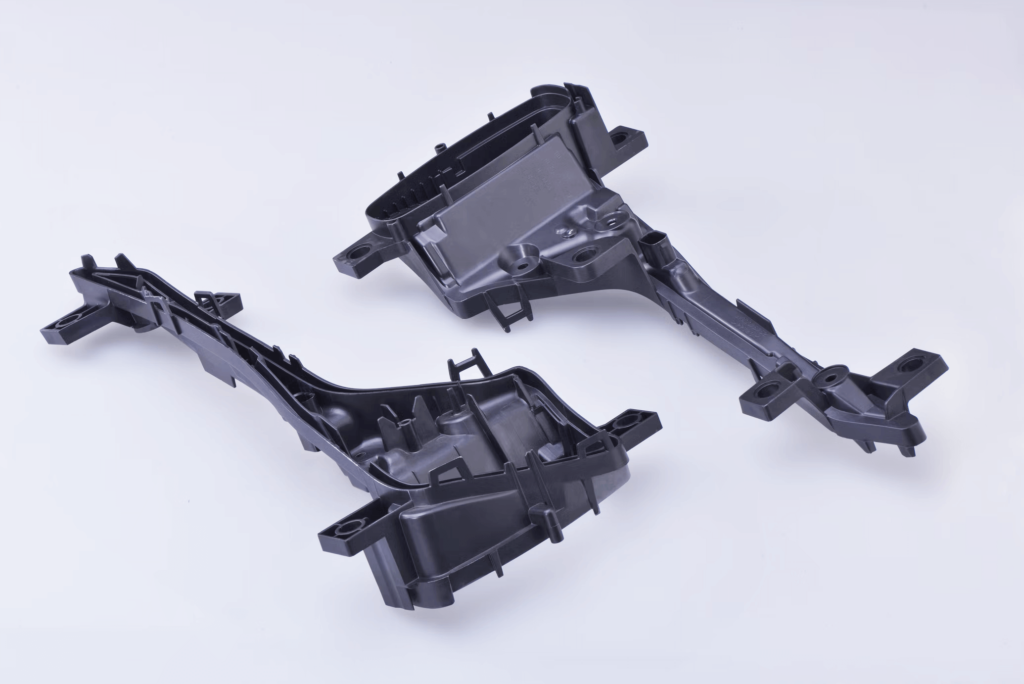
From the injection mold function point of view, that is, to complete the design of pouring system, molding system, heat exchange system, demoulding system, etc.
Although the structure of the mold may vary greatly due to the variety and performance of the plastic, the shape and structure of the plastic products and the type of the machine, the basic structure is the same.
Mould Mould is mainly composed of pouring system, temperature regulating system, molding parts and structural parts. The casting system and molding parts are directly in contact with plastic parts, and change with plastic and products, is a complex mold, change, processing smooth degree and high precision parts.
The mold is composed of two parts: moving mold and fixed mold. The moving mold is installed on the moving template of the forming machine, and the fixed mold is installed on the fixed template of the forming machine.
When forming, the moving mold and the fixed mold are closed to form the pouring system and the cavity. When opening the mold, the moving mold and the fixed mold are separated in order to take out the plastic products.
In order to reduce the heavy mold design and manufacturing workload, most of the injection mold used standard mold.
Injection molding is now a very important way of plastic tool production and processing, and in the use of injection molding processing, there are a lot of factors affecting injection molding processing.
In the process of injection molding, when the plastic material flows out of the static and dynamic surface of the mold, burr phenomenon may occur in some cases. Mold, in addition, injection molding process shrinkage phenomenon is also one of the factors that affect injection molding process is very big, the reason why there will be shrinkage phenomenon in the process of injection molding, mainly because of the processing of raw materials in the middle of the production is too thick, resulting in the surface of the finished product depression phenomenon.
Injection molding is a very important work in the manufacture of plastic products, but also a very complicated work; In the injection molding process, if not fully prepared, any small change, may affect the quality of the product; Moulds, such as plastic, are completely different in liquid state and volume after solidification, so it is necessary to design the details of products in this link.
Notes on mold design and manufacture
1. Glue level inspection
Check whether the glue level is even. If not, it will cause shrinkage and affect the appearance.
2. Determine parting surface and drawing Angle
The parting surface is selected as the large value projected on the direction of the open die to simplify as much as possible.
Touch and wear position: try to choose to touch the rear die. If you want to touch the front die, easy to walk the front, affect the appearance, the use of plane contact.
Pillow position: pillow 5-8 mm, and then flat with the large parting surface, the glue part of 3 degrees, 3 degrees behind, or avoid space.
Insertion position: use side work, pull out 3 degrees, generally do inserts.
3. drawing principle
Die drawing in the direction of glue reduction.
The big end of the shaft is the product size and the small end of the hole is the product size.
4. 2D mirror
2D must pay attention to the mirror and shrink. If you forget this step, most of the mold scrap.
The role of plastic mold processing
There are many places where plastic moulds can be used, and the products processed by it mainly serve the industrial field. Such as the manufacturing and processing industry of all kinds of process equipment, parts, and so on. Of course, some mold processing can also serve the catering industry and other industries in need.
Mold processing can be said to greatly reduce the complex industrial production process. Due to the rate of finished processing products, low consumption has been widely used at home and abroad. Plastic mold injection processing, television shell, washing machine inside the barrel, these are through mold processing and products.
The finished product processed by mold has the characteristics of high precision. Through injection molding, hundreds of thousands or more of the required parts can be processed.
Where should we pay attention to the plastic mold injection molding?
- Raw materials must be fully dry according to demand, without moisture, or the midwife will have material lines on the surface after injection.
- If the temperature, pressure, and temperature of injection molding are not enough, the midwives will lack glue and stick mold during injection molding.
- The material should be cleaned after stopping midway from preventing the material from being degraded in the screw due to the long stay time and forming brittle injection midwives.
- In the process of injection molding, it is necessary for employees to wear clean cotton gloves to prevent the appearance of the product after injection molding from dirty finger marks.