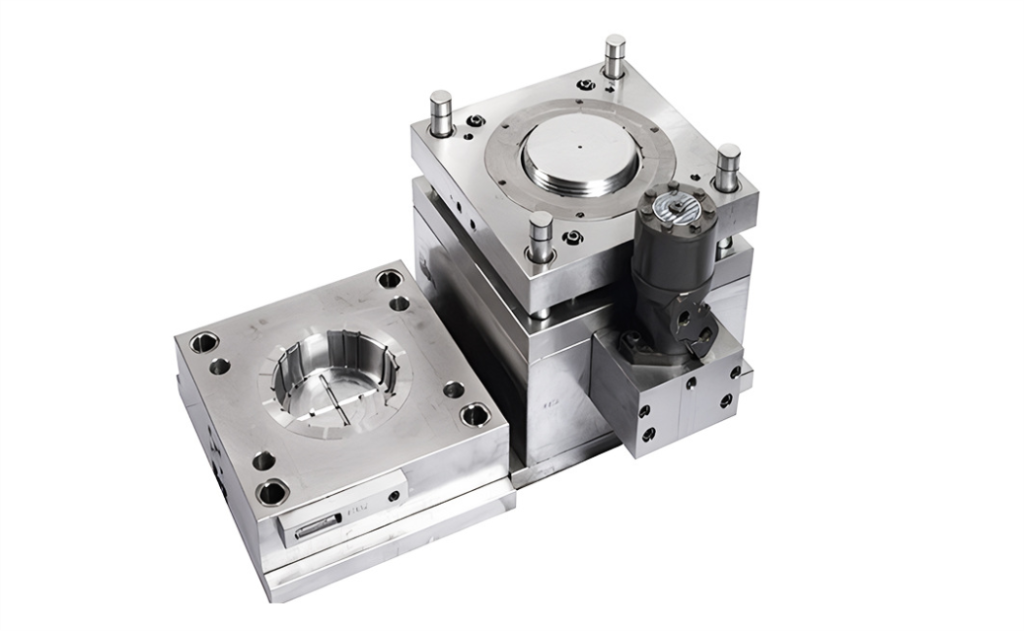
The manufacture of mold generally requires forging, cutting, heat treatment and other processes. In order to ensure the manufacturing quality of die and reduce the production cost, the material should have good malleability, cutting machinability, hardenability, hardenability and grindability. It should also have small oxidation and decarbonization sensitivity and quenching deformation cracking tendency.
About the introduction of mold process performance, let’s have a look.
Forgeability
It has low deformation resistance of hot forging, good plasticity, wide forging temperature range, low tendency of cold cracking and reticular carbide precipitation.
Annealing manufacturability
The spheroidizing annealing temperature range is wide, the annealing hardness is low and the fluctuation range is small, and the spheroidizing rate is high.
achinability
Large cutting consumption, low machining loss, low machining surface roughness.
Notes on mold design and manufacture
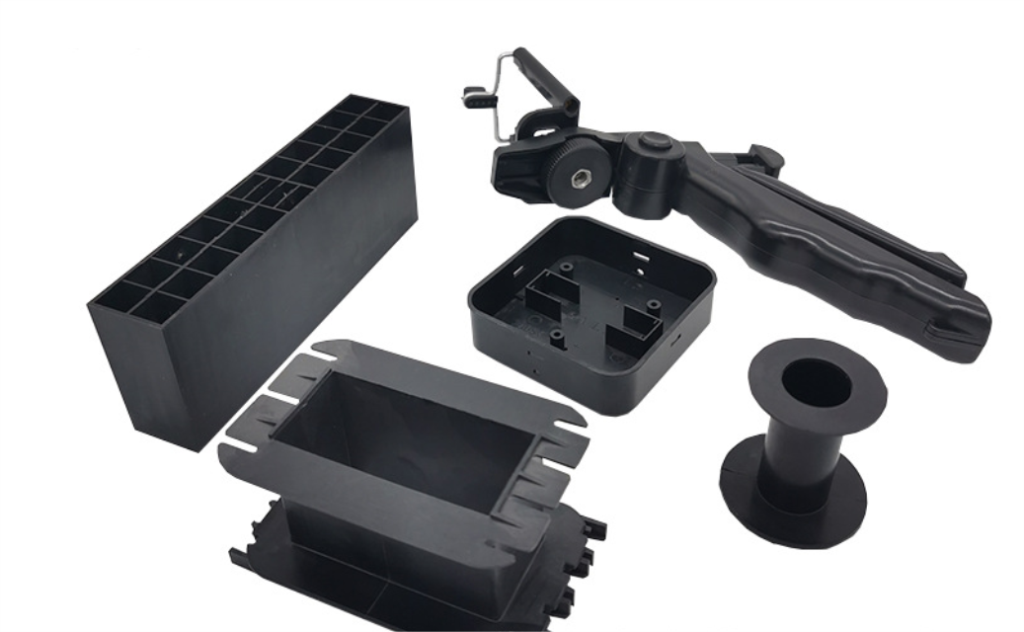
In the process of production, the cooling time of plastic injection parts accounts for about 80 % of the whole production cycle. Poor cooling often leads to warping deformation or surface defects, which affects the dimensional stability of the product. Therefore, reasonable arrangement, pressure retention and cooling time can improve product quality and productivity.
The cooling time of the product is usually the time between the time when the plastic melt has filled the cavity of the injection mold and the time when the product can be opened and removed. Can open a mold to take out the time standard that make a piece, often use a piece to already sufficient solidify, have certain intensity and rigid prevail, when opening a mold top, do not send deformation craze. Even if it is molded with the same plastic, its cooling time is different from the wall thickness, the temperature of the molten plastic and the demoulding temperature of the molding parts and the temperature of the injection mold. The shell of Beijing battery is moulded, so we have no correct cooling time to calculate, we only have a formula for calculation based on appropriate assumptions.
At present, we usually use the following three standards as reference for cooling time:
① The center temperature of the thick part of the wall of the plastic injection processing part, all the time needed to cool down to the thermal deformation temperature of the plastic below;
② The central temperature of the thick part of the wall of the crystallized plastic, all the time it takes to cool down to below his melting point, or the time required to reach the specified percentage of crystallization;
③ The average temperature in the section of plastic injection processing parts, cooling to the specified mold temperature time.
How to make high quality injection molding moulds?
Do mold manufacturers in the production speed at the same time to pay attention to how to ensure quality. Mold processing is a strict enterprise of technology and equipment requirements, just satisfactory here can be said to be very appropriate. Therefore, the enterprise should be strict in technology and management. Aria Manufacturing co., Ltd. is a high quality injection mold supplier, they have more than 10 years of molud manufacturing experience.
For some automobile covering parts, aerospace parts, household appliances, toys and other products, the shape of many products is irregular and mostly for the combination of curved surface, among which the small units of high-precision parts even need to reach mm and μm. This requires a high-precision computer system to complete the design and injection process. To make the error small.